SAP BARCODE SOLUTIONS
digitally transform every aspect of your warehouse.
With a ready-to-go SAP barcode solution, complete with built-in transaction code library, there’s nothing you won’t be able to do.
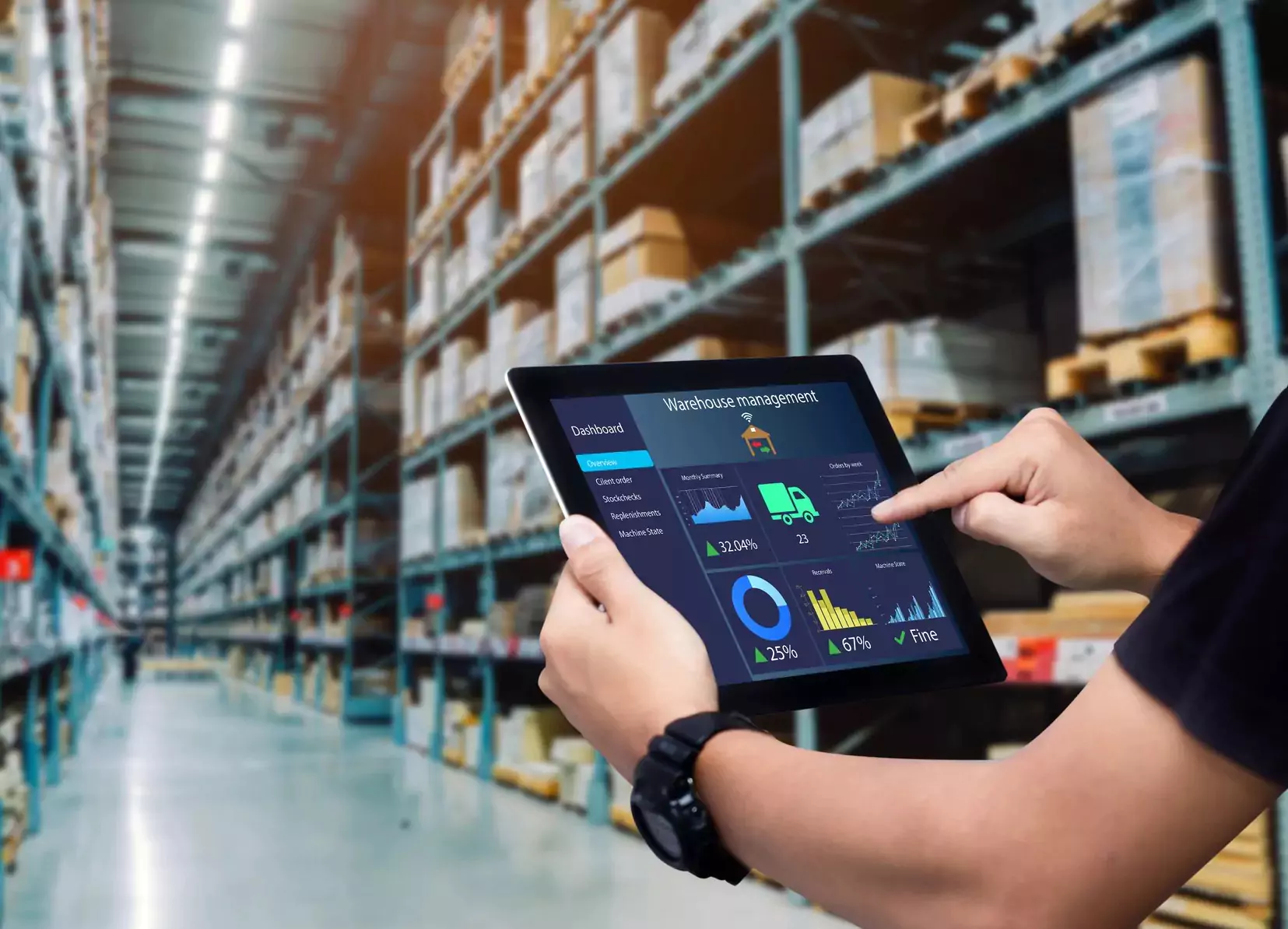
Inventory management
Everything you need, right when you need it.
Make plant inventory management easier, more accurate, and efficient. In a busy warehouse environment, keeping inventory accurate is essential to staying on schedule, preventing delays, and cutting down on waste. Seamlessly integrate your barcoding with SAP to give you real-time updates, smooth stock movement, and create fewer manual tasks. Now, your team can focus on what really matters. With clear visibility into stock levels and locations, you can avoid stockouts, prevent overstocking, and maintain just the right amount of inventory to keep operations running smoothly.
Real-Time Inventory
By updating SAP data as items are moved, used, or received, teams have up-to-the-minute visibility into inventory levels.
Reduced Stockouts and Overstocking
Track inventory usage and replenishment needs in real time so you can avoid both stockouts and excess inventory.
Streamlined Goods Receipts
Simplify the processes of receiving new materials and issuing items for use, reducing paperwork and manual tracking.
Improved Stock Count Accuracy
Barcode scanning reduces human error in inventory counts, so stock records in SAP match the actual items on hand.
Faster Physical Inventories
Barcoding makes physical inventory counts and cycle counts faster and more efficient. Scan items and locations for faster counting.
Efficient Material Transfers
Automatically log material transfers in SAP, making it easy to maintain clear records of where materials are located.
Physical Inventory SAP Transaction codes
MI04 – Physical Inventory Count
The screen prompts the user for the Physical Inventory Document number. It then returns the document count data for verification and prompts for the initial count quantity. Finally, the screen posts the inventory count to the SAP system and notifies the user of the transaction’s success.
MI05 – Physical Inventory Recount
The screen prompts the user for the Physical Inventory Document number. It then returns the document count data for verification and prompts for the new count quantity. Finally, the screen posts the inventory count to the SAP system and notifies the user of the transaction’s success.
MI04/MI05 Combo
The screen prompts the user for the material number. It then returns the current active physical inventory document data and prompts for the count quantity. If the item has been counted, the count quantity will also be displayed for verification. When the user posts the count quantity, the screen automatically checks to determine whether the post should be a count (MI04) or a recount (MI05) posting.
MI09 – Physical Inventory Count Without Reference
The screen prompts users for the storage location and material number. It then returns the material information for verification and prompts for the counted quantity. Finally, the screen creates the Physical Inventory Document in the SAP system along with the inventory count and notifies the user of the transaction’s success.
stock inquiry SAP Transaction codes
MMBE – Plant StOCk per Material
The screen prompts the user for the material number and then returns the inventory for the material in SAP and displays the results. Users have the option to filter the results displayed by plant, storage location, batch, and/or non-zero values. This is a reporting-only transaction and does not include any posting to SAP.
LS24 – Bin Stock per Material
The screen prompts the user for the warehouse, plant, and batch or material number, usually scanned off documentation or packaging. When the user selects the QUERY button, the interface returns all matching Warehouse Quants. Each Quant is shown one at a time. The user can navigate between Quants. This is a reporting-only transaction and does not include any posting to SAP.
Transfer posting SAP Transaction codes
MB1B-301 – Transfer Posting Plant to Plant
This screen prompts the user for the issuing plant, storage location, and material number or batch number. The screen then returns the existing inventory information for verification and prompts for the receiving plant, storage location, and quantity to move. Finally, the screen posts the goods movement to the SAP system and notifies the user of the transaction’s success.
MB1B-309 – Transfer Material to Material
The screen prompts the user for issuing and receiving material, source and destination plant, and storage location. The interface then posts the goods movement to the SAP system and notifies the user of the transaction’s success.
MB1B-311 – Transfer Posting Storage Location to Storage Location
This screen prompts the user for the issuing Storage Location and a material number or batch number. The screen then returns the existing inventory information for verification and prompts for the receiving Storage Location and quantity to move. Finally, the screen posts the goods movement to the SAP system and notifies the user of the transaction’s success.
LT01 – Create Transfer Orders Bin to Bin
The screen prompts the user for the warehouse, movement code, plant, storage location, and batch or material number, usually scanned from documentation or packaging. The screen then prompts the user for the source and destination storage type, section, and bin. Finally, the screen creates a Transfer Order (TO) in the SAP system and notifies the user of the transaction’s success.
LT12 – Picking for Transfer Orders
This screen prompts the user for the Warehouse and Transfer Order (TO) number, usually scanned off documentation or packaging. The screen returns all matching and open (unconfirmed or partially confirmed) TO lines. Each TO line is shown one at a time. The user can navigate between TO lines and mark all desired lines by checking the CONFIRM box for each line. Finally, the screen posts a confirmation containing all selected lines to the SAP system and notifies the user of the transaction’s success.
LT12 – Putaway for Transfer Orders
The screen prompts the user for the Warehouse and Transfer Order (TO) number, usually scanned off documentation or packaging. The interface returns all matching and open (unconfirmed or partially confirmed) TO lines. Each TO line is shown one at a time. The user can navigate between TO lines and mark all desired lines by checking the CONFIRM box for each line. Finally, the screen posts a confirmation containing all selected lines to the SAP system and notifies the user of the success of the transaction.
PURCHASING AND RECEIPT SAP Transaction codes
MB01-101 / MIGO-101 – Goods Receipt for Purchase Order
This screen prompts the user for the Purchase Order number and/or a material or batch number, usually scanned off the delivery documentation or packaging. The screen then returns the matching line item information for verification of quantity and receiving location. Finally, the screen posts the goods movement using Movement Type 101 (Receipt to Warehouse/Stores) to the SAP system and notifies the user of the transaction’s success.
MB1C-501 – Goods Receipt without Purchase Order
The screen prompts the user for the material number, usually scanned from the delivery documentation or packaging. The screen then returns the material information for verification and prompts for the quantity and receiving location. Finally, the screen posts the goods movement using Movement Type 501 (Receipt without Purchase Order into Warehouse) to the SAP system and notifies the user of the transaction’s success.
case study
Keeping count across multiple locations.
A national chemical and lubricant company defined a limited number of storage locations in their SAP environment to keep things simple. Unfortunately, at audit time, this posed some major problems.
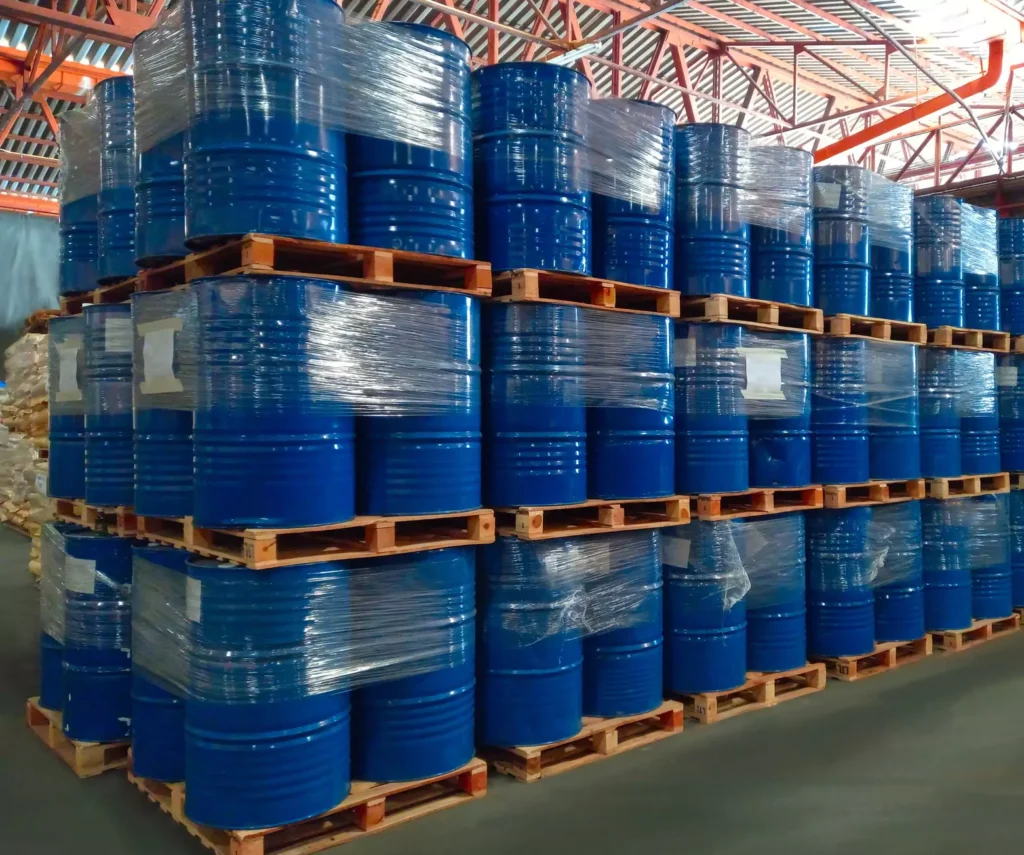
Order Management
Power your production workflow.
Make managing manufacturing orders simpler and more efficient. With all the details of each order—from materials needed to where the finished product goes—tracked in one place, connecting data with SAP takes the hassle out of production management. By scanning materials as they’re used and logging finished goods right when they’re completed, teams get an up-to-the-minute view of inventory. This real-time tracking helps prevent stockouts, avoids delays, and keeps production flowing smoothly. No more manual data entry or wondering if you have what you need to get the job done. You know you have it covered.
Visibility Across Production Stages
ofWith instant updates, managers and operators have a clear view of materials and finished goods at each stage of production.
Smooth Production Orders
Simplify every step of the production order, reducing manual data entry and making it easy to see what’s needed and what’s done.
Reduce Risk of Delays
With accurate inventory data and real-time updates, you can ensure materials are available when needed to support the production schedule.
Simplified Goods Receipt and Issue
Scans record both the materials taken for production and the finished goods as they’re completed, making it easy to keep track of goods in and out of inventory.
Accountability and Accuracy
A barcode system tracks every step, making it easy to ensure accurate inventory and clear accountability for materials used in production.
Efficient Inventory Management
By automating inventory tracking for both materials used and products created, you’ll reduce manual errors, avoid overstocking, and optimize inventory costs.
Order management SAP Transaction codes
MB1A-261 – Goods Issue to Production Order
Prompts the user for the Production Order number, usually scanned off the order documentation. The screen then returns the matching line item information for verification of quantity and issuing location. The user can navigate between items. Finally, the screen posts the goods movement using Movement Type 261 to the SAP system and notifies the user of the transaction’s success.
MB31-101 – Goods Receipt for Production Order
Prompts the user for the Production Order number and/or a material or batch number, usually scanned off the delivery documentation or packaging. The screen then returns the matching line item information for verification of quantity and receiving location. Finally, the screen posts the goods movement using Movement Type 101 to the SAP system and notifies the user of the transaction’s success.
CO11N – Goods Receipt for Production Order
The screen prompts the user for the Production Order number and a specific operation, usually scanned from the order documentation or packaging. The screen then returns the matching line item information for verification and prompts users for the quantity to be confirmed. Finally, the screen posts the confirmation to the SAP system and notifies the user of the transaction’s success.
CO15 - Production Order Confirmation on Header Level
This screen prompts the user for the Warehouse and Transfer Order (TO) number, usually scanned off documentation or packaging. The screen returns all matching and open (unconfirmed or partially confirmed) TO lines. Each TO line is shown one at a time. The user can navigate between TO lines and mark all desired lines by checking the CONFIRM box for each line. Finally, the screen posts a confirmation containing all selected lines to the SAP system and notifies the user of the transaction’s success.
Shipping & Receiving
deliver your product with confidence.
Bring simplicity and accuracy to your shipping and receiving processes. Manage outbound deliveries with ease. Keep track of goods as they’re shipped or received. Meet customer expectations and maintain an efficient workflow. Use a simple two-way connection with SAP to streamline these processes and allow your team to create and track outbound deliveries with quick barcode scans. This system helps you manage everything from order picking to transportation scheduling, making sure each shipment is tracked and documented at every step. With instant updates and easy access to shipping details, your team can stay on top of all shipping and receiving activities, reducing errors and keeping operations running smoothly.
Easily Track Outbound Deliveries
Quickly create and track outbound deliveries, making sure every item is documented as it leaves your facility.
Accurate Shipping Notifications
Automatically generate shipping notifications and delivery notes to ensure smooth handoffs along the supply chain.
Simplified Transport Scheduling
Once an outbound delivery is created, teams can schedule transportation to keep shipments on time and reduce bottlenecks.
Easy Order Picking
Barcode scanning makes it easy to pick items for shipping, reducing the risk of mistakes and ensuring the right products are sent every time.
Efficient Receiving
Barcode scans log items into inventory immediately, making it easy to verify shipments and keep stock levels up to date.
Supply Chain Visibility
With all data updated in real time, your team knows where goods are at, helping with planning and ensuring timely deliveries.
SHIpping & Receiving SAP Transaction codes
VL01N – Create Outbound Delivery for Sales Order
The screen prompts the user for the Sales Order number and a material availability date. It then verifies that an active outbound delivery document does not exist and returns the matching line item information for verification. Finally, the screen posts the request to the SAP system and notifies the user of the transaction’s success.
VL1OB – Create Outbound Delivery for Stock Transport Order
The screen prompts the user for the Stock Transport Order number and a material availability date. It then verifies that an active outbound delivery document does not exist and returns the matching line item information for verification. Finally, the screen posts the request to the SAP system and notifies the user of the transaction’s success.
VL02N – Post Goods Issue for Outbound Delivery with Reference to Sales Order
The user provides a Delivery number, usually by scanning a barcode from printed documentation. It looks up the delivery in the SAP system and retrieves all unissued line items. For each line, the screen shows information from SAP, including the picked quantities. The screen does not provide any editing capabilities, assuming picking already took place on the WM side. Finally, it posts the goods issue for the delivery to the SAP system and notifies the user of the posting’s success.
case study
real-time data delivery to speed up product delivery.
A manual goods receipt process caused delays in shipping and slowed down order delivery times. To better coordinate shipping orders with delivery driver availability, the customer needed real-time data.
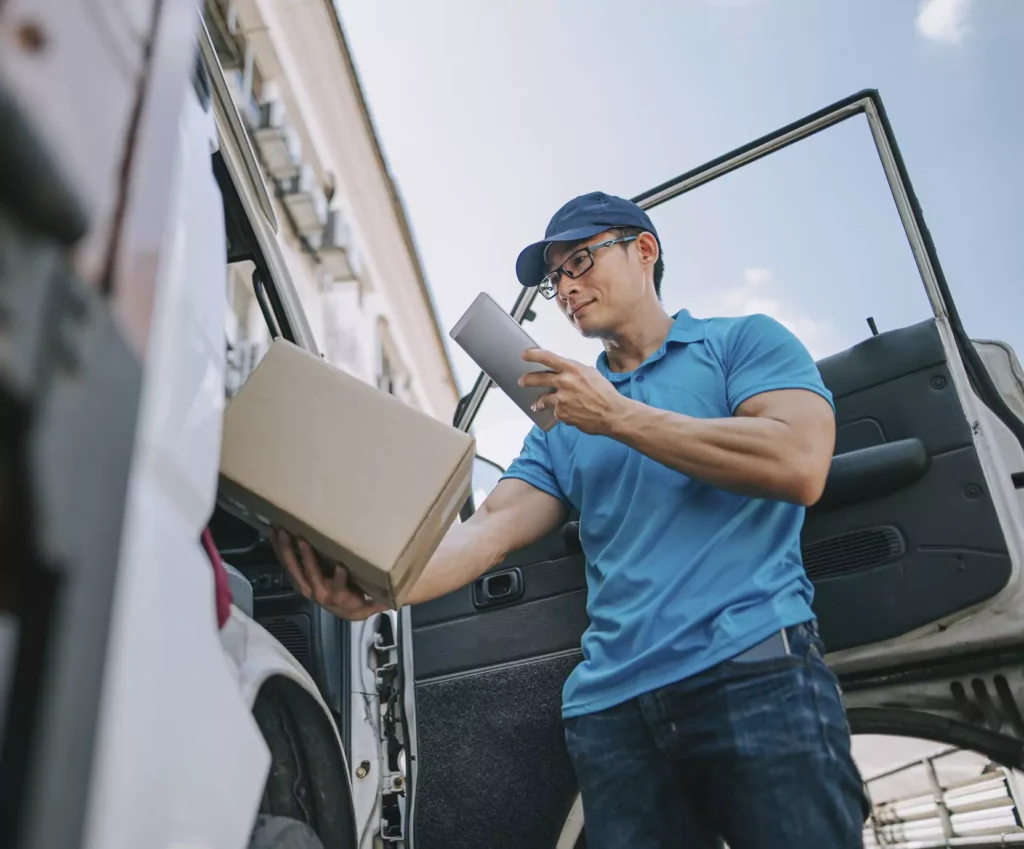
Plant Maintenance (MRO)
Make the move to
proactive maintenance management.
Plant maintenance requires careful tracking of assets, spare parts, and maintenance orders, all of which are managed more efficiently with a direct connection with SAP. Creating a barcode solution transforms how your maintenance teams handle materials, track usage, and manage inventory. This doesn’t just simplify day-to-day tasks—it also supports a proactive maintenance strategy, helping you prevent issues before they start. Start saving yourself time and costs on repairs and downtime.
Streamlined Work Orders
Barcoding helps maintenance teams quickly pull up work orders, scan parts and tools, and log usage directly in SAP.
Real-Time Inventory
As technicians use or relocate parts, barcodes automatically update SAP records in real time, keeping inventory data accurate.
Spare Parts Tracking
Inventory management for spare parts allows precise tracking of all assets used for maintenance and repairs.
Enhanced Preventive Maintenance
By keeping accurate records of parts used and equipment serviced, barcoding helps organizations identify patterns in maintenance needs.
Reduction in Manual Errors
Technicians can quickly scan parts and work orders, minimizing inaccuracies and ensuring that records reflect actual work done.
Improved Cost Management
Support better budget forecasting for maintenance activities to reduce unnecessary purchases and optimize stock levels.
Plant Maintenance SAP Transaction codes
IW31 – Create Maintenance Orders
Prompts users for a technical object number (Equipment or Functional Location). The screen validates the input technical object number and creates a maintenance order based on a pre-defined set of defaults that the user can change.
IW41 – Time Confirmation for Work Order
Prompts users for their personnel number and the work order number. The screen will validate the input information against SAP, and, if valid, will display the work order operations for the user to select.
Once the operation is selected, users can choose ‘Start’ or ‘Complete’. When the user chooses ‘Start’, the screen will capture the current date/time for later processing. When the user selects ‘Complete,’ the screen will post the data to SAP for time confirmation against the input work order and operation.
IW3K – Add Components to Work Order
Prompts the user for the order number, usually scanned off the order documentation. The screen validates the order number and, if valid, returns the order operation (to which the components will be assigned) on the display for users to select.
Once the operation is selected, the screen prompts the user to scan the material number(s) to be added to the order along with the quantity. When the user selects the ‘Post’ button, the screen posts the material number(s) to the SAP work order. Options to validate plant and storage location and link directly to MB1A-261 are also available.
IW22 – Maintenance Notification Update
This screen allows users to update an existing maintenance notification. The screen prompts the user to provide the notification number. If the scanned value is valid in SAP, the remaining input fields will be enabled for the user to add additional data. When the user chooses the ‘Post’ option, the screen will post the data to SAP to update the notification.
MB1A-261 – Goods Issue Work Order
The screen prompts the user for the Work Order number, which is usually scanned from the order documentation. The screen then returns the matching line item information for verification of quantity and issuing location. The user can navigate between items. Finally, the screen posts the goods movement using Movement Type 261 to the SAP system and notifies the user of the transaction’s success.
MB1A-262 – Goods Issue Reversal
The screen prompts the user for the Work Order number, usually scanned from the order documentation or packaging. The screen then returns the matching line item information for verification. The user can navigate between items. Finally, the screen posts the goods movement using Movement Type 262 to the SAP system and notifies the user of the transaction’s success.
MM02 – Set Bin Location
The screen prompts the user for the material number, plant, and storage location. Based on the input data, the screen validates and retrieves the current storage bin description in SAP. If the user changes this value, the screen updates the storage bin data in the material master Plant/SLoc Bin Location. The bin location will then be visible in the SAP inventory view.
case study
keeping track of critical maintenance schedules.
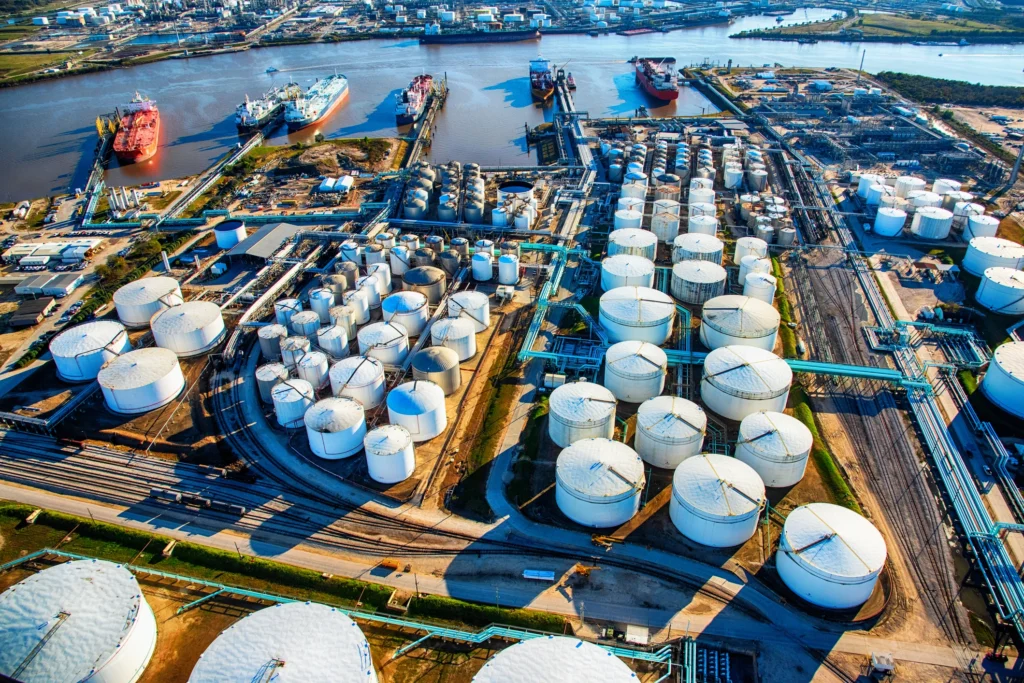
Asset Tracking
No more guesswork or lost materials.
Make tracking your manufacturing assets simple and precise. Easily enable your team to keep up with asset locations, quantities, conditions, and maintenance needs. With barcode tags and mobile readers, staff can quickly check asset details, update statuses, and generate reports as needed, all integrated with SAP. This system helps reduce unnecessary purchases, prevent losses, and even optimize tax calculations by accurately tracking depreciation. By supporting proactive maintenance, Junot’s barcoding solution extends asset life, reduces replacements, and makes operations more efficient and cost-effective.
Asset Lifecycle Management
The system supports assets from creation to retirement, allowing teams to update locations, track usage, and schedule maintenance.
Asset Location Tracking
Teams can quickly locate assets
within the facility, minimizing downtime spent searching for equipment.
Accurate Quantity and Condition
Easily track how many of each asset you have and verify their condition, helping to prevent unexpected breakdowns.
Streamlined Depreciation Tracking
With up-to-date data on asset condition and age, you can support more accurate tax calculations based on depreciation schedules.
Loss Prevention and Audits
Asset audits with mobile barcode readers help companies conduct regular inventories to track equipment and prevent losses.
Avoid Unnecessary Purchases
Optimize your budget and storage space with accurate visibility into what’s available, avoiding duplicate or unneeded equipment purchases.
Fixed Asset Tracking SAP Transaction codes
Create / Update Fixed Asset
The interface prompts the user for a Company Code, Asset number, and, if necessary, an Asset Sub number. This transaction will first validate to see if the asset exists in SAP. If the asset exists, details for the asset will be displayed for users to edit. If the asset does not exist, the interface will create a new asset using data from a pre-defined asset as a reference. After the asset is created, details of the created asset will be displayed for users to edit, with the input Asset Number – Sub number posted as the Inventory Number.
Inventory Fixed Asset
The interface prompts the user for a Company Code, Asset number, and, if necessary, an Asset Sub number. This transaction will validate that the asset exists in SAP, and if so, will display asset details for users to view. Upon posting, this transaction will update the asset’s Last Inventory Date, along with the Inventory note.
Transfer Fixed Asset – Intra Company
The interface prompts the user for a Company Code, Asset number, and, if necessary, an Asset Sub number. This transaction will validate that the asset exists in SAP, and if so, will display additional asset transfer details for users to enter. Upon posting, this transaction will post an intra-company asset transfer.
Transfer Fixed Asset – Inter Company
The interface prompts the user for the Source (original) Company Code, Asset number, and, if necessary, an Asset Sub number. This transaction will validate that the asset exists in SAP in that company code and, if so, display additional asset transfer details for users to enter. Upon posting, this transaction will post an inter-company asset transfer.
Retire Fixed Asset without Revenue
The interface prompts the user for a Company Code, Asset number, and, if necessary, an Asset Sub number. This transaction will validate that the asset exists in SAP and, if so, prompt the user for a short description of the reason for retirement. Upon posting, this transaction will default to the current date as the asset value date for retirement.
Retire Fixed Asset with Revenue
The interface prompts the user for a Company Code, Asset number and, if necessary an Asset Sub number. This transaction will validate that the asset exists in SAP, and if so, will prompt the user for the Revenue value, and a short description as the reason for retirement. Upon posting, this transaction will default to the current date as the asset value date for retirement.
Block Fixed Asset
The interface prompts the user for a Company Code, Asset number, and, if necessary, an Asset Sub number. This transaction will validate that the asset exists in SAP. Upon posting, this transaction will set the asset status to block (or lock). Note: A block status on the asset keeps the asset values from changing for end-of-period depreciation calculations. Asset transfers and retirement postings are still possible. This is typically used when an asset is to be sold, or to prevent future postings to an asset under construction once the project is complete.
Delete Fixed Asset
The interface prompts the user for a Company Code, Asset number, and, if necessary, an Asset Sub number. This transaction will validate that the asset exists in SAP. Upon posting, this transaction will delete the Fixed Asset from the system. Note: Deleting assets is sometimes necessary to remove old assets (legacy assets from previous systems) after an Asset Transfer transaction. Fixed Assets can only be deleted when no postings have been made.
Fixed Asset Reports
Download Fixed Asset Inventory List
The interface prompts the user for a Company Code and fiscal year. This transaction will retrieve the list of Fixed Assets in SAP with the setting “include the asset in inventory list” set to TRUE. The interface for Fixed Assets then retrieves a list of Fixed Assets that fit the entered criteria. The list will be displayed for the users to view, along with an option to email, or to output locally to a delimited format file.
Missing Fixed Asset Inventory List
The interface prompts the user for a Company Code and a fiscal year. This transaction will retrieve the list of uninvented Fixed Assets in SAP. The list will be displayed for users to view, along with an option to email or output locally to a delimited format file.
Inventoried Fixed Asset Inventory List
The interface prompts the user for a Company Code and a fiscal year. This transaction will retrieve the list of Fixed Assets in SAP inventoried as of the current date. This list will be displayed for users to view, along with an option to email or output locally to a delimited format file.
Blocked Fixed Asset Inventory List
The interface prompts the user for a Company Code and fiscal year. This transaction will retrieve the list of Fixed Assets in SAP with the Acquisition Lock flag set to TRUE. The list will be displayed for the users to view, along with an option to email or output locally to a delimited format file.
Retired Fixed Asset Inventory List
The interface prompts the user for a Company Code and a fiscal year. This transaction will retrieve the list of Fixed Assets in SAP with Last Retirement Date within the input fiscal year. The list will be displayed for the users to view, along with an option to email or output locally to a delimited format file.
case study
Reacting fast so production doesn’t slow down.
A multinational corporation had a 30-day window to implement a barcoding solution for their recent SAP upgrade. The selected platform needed to be flexible, scalable, and work with existing software.
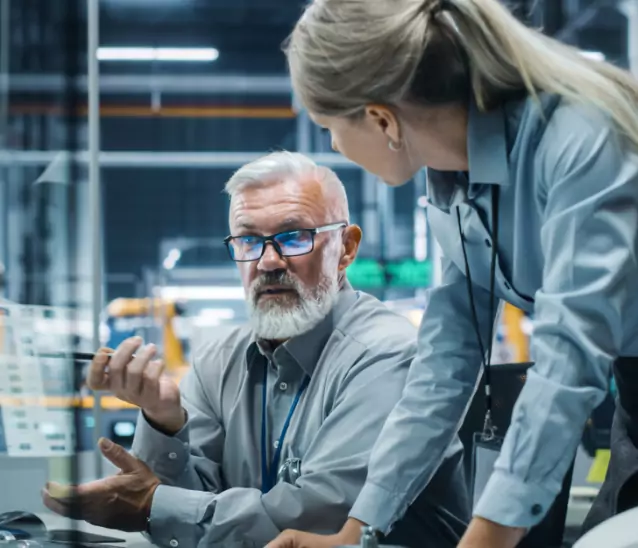
Why junot systems
We’re sap experts so your warehouse team doesn’t have to be.
Decades of SAP Experience
Junot Systems’ SAP integration solutions have been in the market for more than 25 years. We’ve seen countless SAP configurations and environments. That experience helps us evaluate your setup and unify your systems quickly.
We Get Warehouses
We specialize in the manufacturing industry, supporting its unique challenges and workflows. Our solutions are tailored to the demands of manufacturers, which translates to smoother implementation, higher efficiency, and integrations that truly connect the warehouse, plant floor, and SAP.
No Custom Code Needed
The barcode to SAP integration is built from the ground up to be a stable, reliable zero-code solution that requires nothing to be installed into your SAP landscape. It also doesn’t require anything installed on the scanning hardware.
Global Hardware Flexibility
Our barcode solution is compatible with any device that runs an HTML5 browser, whether it’s a desktop, tablet, or phone. This versatility means you’re not locked into specific hardware, providing flexibility and options that fit your team’s unique needs.
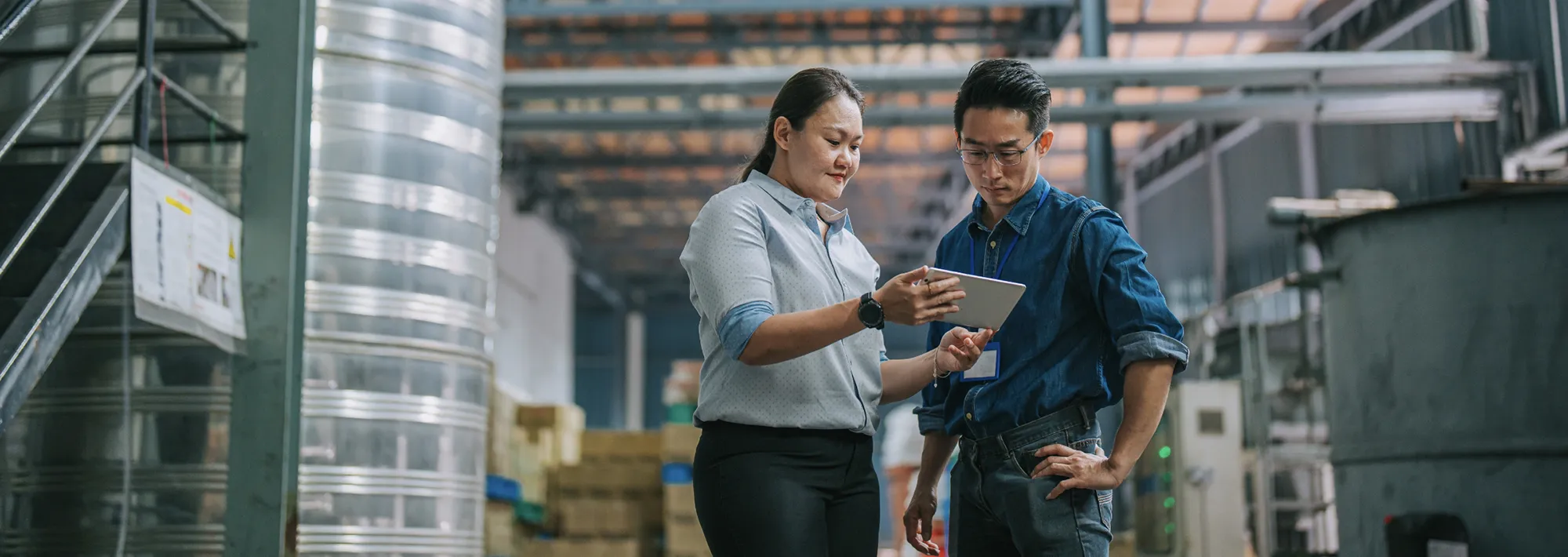
SAP Barcoding Resources
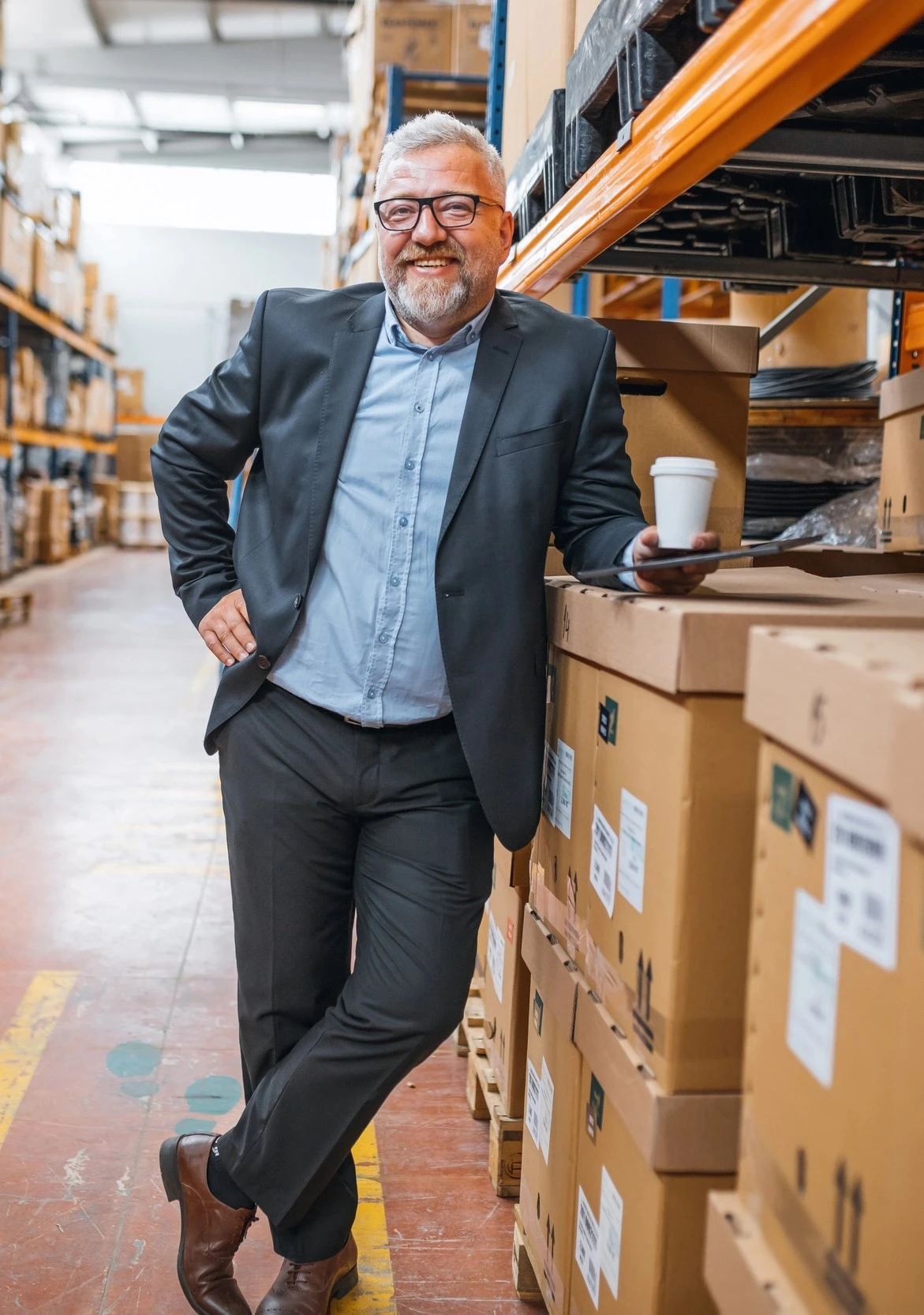
Getting started is so simple
transform your warehouse management in minutes.
Talk with Certified SAP Experts.
Let our team know what you want to accomplish and what you’re trying to solve. They’ll guide you through your options.
Connect Everything in Minutes.
We’ll get you configured and connected in minutes. No custom code or hardware applications necessary to communicate with SAP.
Get a Good Night’s Sleep.
Count on your warehouse-to-SAP connection for accurate and efficient data collection with real-time updates and confirmations.